FIABLE ANTI-CORROSION COATING
- fiable
- Mar 1, 2024
- 1 min read
Carbon steel fastener is susceptible to corrosion and rust is inevitable if produced without surface treatment process during manufacturing to provide a protective layer. Corrosion can be caused by industrial pollution, moisture or salt particles in coastal environments or sand with moisture in desert environments.
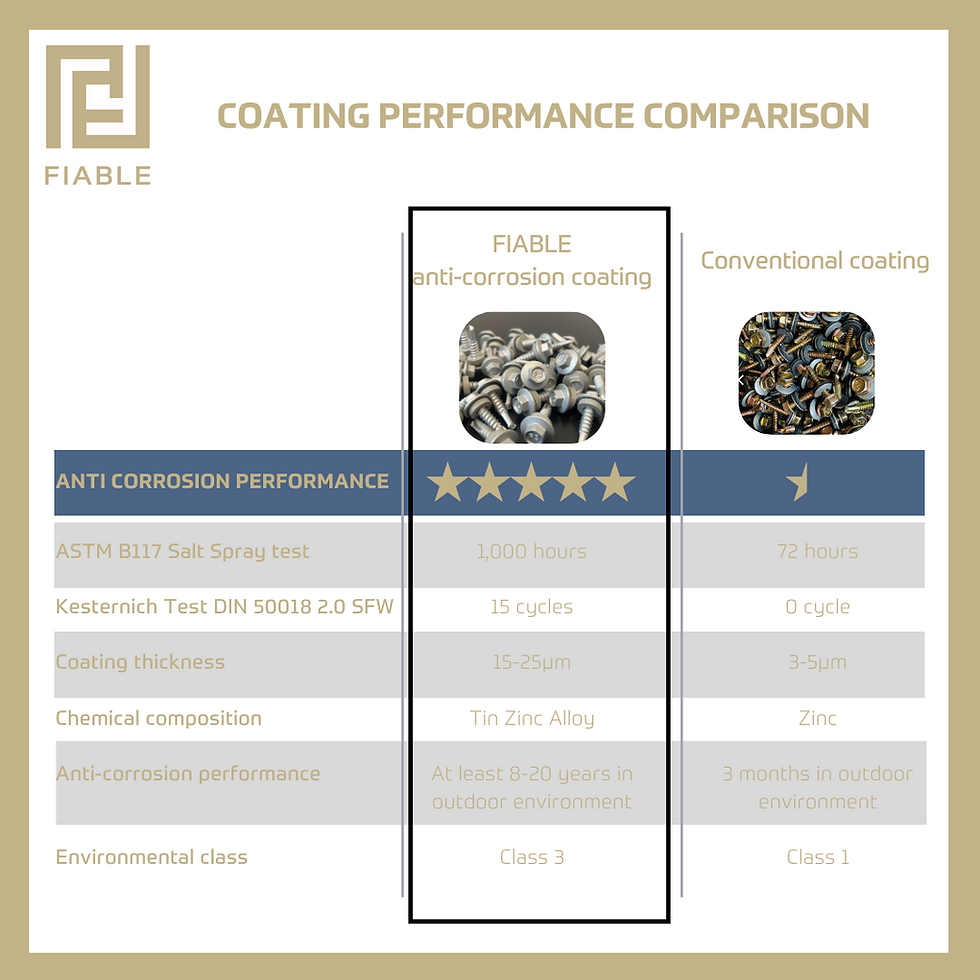
Corrosions of carbon steel fasteners can lead to failure and or collapse of systems components due to material premature deteriorations thus
anti corrosion coating of fasteners used in buildings, constructions and general applications is crucial as they provide integrity and security to the overall system components.
Even if a screw is used for internal applications, it may be exposed to a corrosive environment during the construction process. Some indoor application fasteners are exposed to moisture over their service life when installed in areas such as bathrooms and kitchens.
It is also important to consider ease of access, as maintenance or repairs to fasteners may be impossible once the construction of the building is completed.

FIABLE anti corrosion coatings offer different grades of protective coatings to suit a wide range of environmental conditions.
Our coating specification complies with Australian Standards AS3566.2 Self-drilling screws for the building and construction industries- corrosion resistance requirement
FIABLE anti corrosion coating can be used in different environmental category classified under International Standard ISO9223:2012 Corrosivity of Atmosphere, Classification, determination and estimation.
When selecting anti corrosion coating class for fasteners, balancing between economy, aesthetic aspects and the environmental conditions with lifetime expectancy are important considerations.
Speak to us to find out the different coating class FIABLE offers to suit your projects requirements and environmental category classifications! Email: ericlim@fiablej.com
Comments